Lalan Group model: Treating workers with respect, dignity
SAPUMALKANDE, Deraniyagala – When workers at the nursery at Lalan’s rubber plantation at Deraniyagala, some 55 km off Avissawella, achieved target production of plants, they were in for a surprise.
One morning a luxury bus turned up and took the 30-plus workers on a trip they would never forget.
Nishantha Seneviratne, General Manager of Lalan Plantations’ Sapumalkande Group said that the company had promised to reward workers if they achieved the target. “To their pleasant surprise a luxury AC bus (we arranged) turns up and they go for day/night trip to Kataragama and have a good time,” he said walking around the well-maintained nursery.
The Sapumalkande nursery has 250,000 plants on average (at any time) of which 100,000 are used by the group and the balance sold to others. This is said to be the best rubber nursery in Sri Lanka.
The vision of the group is to become a world class natural rubber plantations management company by 2014.
Sri Lanka’s plantation sector, particularly tea, is grappling with problems of rising costs and a labour shortage – and looking for new ways to replace the British model. Recently an India-based Tata Group official related, at a human resources management forum in Colombo, how the company had turned around its crisis-hit tea plantations (facing issues similar to Sri Lanka) with a worker-management-style which eventually led to some workers becoming directors and involvement in the operations of the company.
On the other hand rubber in Sri Lanka is on a better wicket with improved prices.
It is in a currently-tested model that the 72-year-old old Lalan Group and its 7,000-strong workforce are showing the way in managing 7,800 hectares of plantations in an efficient and productive profitable way.
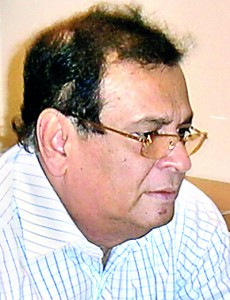
Gayan Samarakone
Gayan Samarakone-Director/CEO of the company, a veteran planter, says that the company’s new model is aimed at increasing yields, productivity and workers’ income levels.
“We engage with workers. Make sure they are part of the decision-making process. Together we come up with ideas, tackle problems, find solutions,” he told the Business Times at the group’s headquarters in Kirullapone near Nugegoda.
The group aims to combine the earlier British model of plantation management with modern trends, demands and needs. “We need to ask ourselves as to how we can improve on what the British gave us. We have this huge asset. How do we come up with new techniques and increase incomes? Unions look after worker interests but on our own we need to treat workers with respect, give them responsibility, some ownership so that they become part of the success. There should be some dignity in what they do,” he explained.
He said for wealth creation to happen to workers and villagers in the vicinity of a plantation, the trickle-down effect should take place.
The highest rubber productivity is in Thailand, Malaysia and parts of India, and here at Lalan plantations the company is aiming to improve yields to over 2,000 kg once the new clearings start yielding.
The company has improved the per capita income to a level not seen in most other plantations resulting in Lalan’s having a waiting list for those keen to be get jobs. “When workers say they are at Lalan’s, there is some recognition,” he added. Management has been decentralized to a level where decisions are made on the ground/on the plantations rather than at head office.
The company plans to replant 200 hectares per annum and plant more trees per hectare. “We need to get 5 kg per tree per annum – that is 2,500 kg per hectare from 450-500 trees. Now we get 1,300-1,400 kg per hectare,” he added.
That management and workers are united in improving and developing the estates is evident from a recent Business Times visit to Lalan’s Deraniyagala estates. Union leader Narayan Ramaraj says he can call the general manager at any time to discuss an issue. “I give him a mis-call on the mobile and he calls back,” he said at the nursery.
“There are issues but we work with management to solve them. We have 30 days of work unlike other estates,” he said, adding that wages are paid on time and the festival advance (earlier in the year) was paid on time.

View of the nursery
Mr Ramaraj said workers get between Rs 28,000 to Rs 30,000 for two wage earners in a family and life is generally reasonable. “In our plantations at least 13-14 workers have 3-wheelers. There are workers who also own motorbikes.”
At the nursery, K.K. Jayatillake, Central Rubber Nursery officer says it takes six months to grow a plant to its full potential.
The nursery is 15 years old and gets lots of visitors from abroad and foreign government officials.
Showing a tree and discussing its tapping potential, Mr Seneviratne says they use a time-tested process of tapping once in three days instead of daily which has resulted in more improved efficiencies, higher yields and maximize use of labour. This year staff got an annual bonus of Rs 60,000 to-Rs 90,000 for staff while workers get an average Rs 15,000 annual bonus.
New clearings are coming up all over at and at one location Roshan Aruna, a junior field officer, explains that 8.4 hectares have been cleared by his team.
“It took a year to clear this area and the 4,300 rubber plants here will take five years to grow to the level when it can be tapped. The plants grow at the rate of four inches per year and at 20 inches we can start tapping,” he said.
The group says it’s ethically committed to sustainable forest management.
“We are of the firm belief that our long- term viability and existence depends on operating in a way that ensures and enhances economic viability, that guarantees the potential of the forest to regenerate itself and is acceptable to society,” it said.
It has a vision of Long term Sustainable Forest Management, which is motivated by its desire to have Forest Stewardship Council (FSC) certification.
Strategies include preserving, nurturing and protecting the environment while harvesting the forestlands with productive plants, and managing a successful business enterprise that benefits the community by providing jobs and at the same time preserving the nature for future generations.
Follow @timesonlinelk
comments powered by Disqus