Breathing life to ancient art
Lacquerwork is an art that commands attention. Whether it is the intricately painted wooden boxes and ornaments that adorn our homes or the boldly striped windows and railings of the Temple of the Tooth, the art form reflects the island’s history and heritage.
Lacquerwork or ‘laaksha’ is the art of painted woodwork. But the intricate detail we imagine to be the product of paint pots and brushes is in fact ‘painted’ without the use of a brush by scraping or carving the surface in order to create the rainbow patterns.
While echoing the grandeur of Kandyan architecture, the humble beginnings of this quintessentially Sri Lankan industry go back to the very heart of village life. Lacquerwork has its roots in the hills of Kandy and Matale and also in Angul Maduwa, Matara. Sadly, it faces a fate similar to most of the country’s dying art forms with the village of Pallehapuvida, Matale being the only one of the original three still dedicated to it. Cue in the National Crafts Council which has worked vigorously to revive the craft, re-introducing lacquerwork to Angul Maduwa.
Off the Tangalle road through Beliatte and into the lush rustic surroundings of Angul Maduwa, we reach a lone white washed building amidst the quiet of the village. In a large airy room, 12 women seated at a work bench or on the floor operating the most unusual of machines are watched closely by a small made gentleman walking around giving pointers and ideas.
For Jagath Wijeratne the past month has kept him from his home in Matale but brought him closer to his profession as a lacquer craftsman. His knowledge and training came from his family; he started lacquerwork while in school, under the tutelage of his uncle. Having been in the industry for 26 years and worked in Colombo and Matale, Wijeratne was sent through the Craft Council to Angul Maduwa to retrain its villagers in an art which they were once masters of. Having worked with them now for a month, he finds the interest and enthusiasm of his ‘pupils’ is overwhelming. “It takes about two years to become a professional, but we are trying to speed up the process.”
The finished goods on the shelves of any Laksala are the outcome of hours, even days of hard work and patience. Production is time consuming -hours spent carving and polishing the wood before applying the lacquer. The workers handle different areas of production, learning how to carve and apply the lacquer. The wood is obtained from the village itself with Kottamba trees being common. The outer bark is stripped before the wood is carved and smoothed into items like boxes, flutes and other curios.

NCC Chairman Buddhi Keerthisena
The painting process is probably the most unusual – done using a kind of lathe, bow and sans paint brushes. The lacquer itself is not the typical liquid based paint but is made of Shellac; a solid heated over a low flame until melted, to a gooey consistency. The melting lacquer has to be stirred over the fire for at least half an hour till it is completely softened. It is then poured over a piece of wood over which it can be then spread. The worker shapes and sculpts the object using a simple lathe fixed to the ground with the help of a bow which is pulled back and forth to rotate it. The ‘painting’ is then done by applying the lacquer onto a piece of wood which is held to the rotating object.
The colourful distinctive geometric patterns which make lacquer work so unique are done in two different ways. ‘Niyapotten-Weda’ or fingernail work is the method used in Matale. Red, yellow, black, and green colours are heated and drawn into thin threads and applied onto the object while using fingernails to carve out the patterns. It is then heated and polished with an Ola leaf to give it a smooth finish.
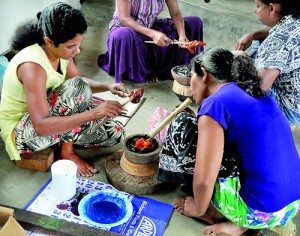
Angul Maduwa: Where a group of aspiring craftswomen are involved in saving a dying tradition. Pix by Ranjith Perera
For now the women of Angul Maduwa use carving knives to scrape out designs on the outer layers.
A maker of musical instruments, Sarath Gamage is one of the regular visitors to the building for these scenes remind him of his childhood. “As a child I saw the last of our village people do this,” he recalls describing the time when Angul Maduwa was famous for its lacquerwork.
Walking around the room, examining the semi-finished goods is Chairman of the NCC Dr. Buddhi Keerthisena who makes regular visits to his new project. Established under the National Craft Council and Aligned Institution Act 1982, the Council works to protect the crafts and the livelihood of the traditional craftsmen. “Most of the artists are in Kandy, Matale and Kurunegala but Angul Maduwa was where it was done in a big way,” he says. Renowned for his work in the batik industry Dr. Keerthisena has worked diligently with the Council to promote and revitalize traditional Sri Lankan crafts.
Having seen success at Colombo Fashion Week he says, “We want to modernize it and bring it up the same way we have done with other industries. First they have to learn and create a good foundation. Then we will introduce new designs.”
The villagers too are energised. Mrs. Gamage, a housewife sees it as a way for women to earn a little money and Sunethra and Rupika, also housewives find their work offers them a new freedom. Like most of the 30 workers they were unemployed and housebound, and never imagined they could become artists. One month later their bold detailed work on boxes shows that they are well on their way.
Processing lacquer
Although the craft is all about painting, the pigments used is ‘Shellac’ which is made from a secretion called ‘lac’ or ‘lakada’ from lacquer insects (Kerrialacca) who deposit the resin on shrubs and branches of trees. The resin is collected, refined and heated with mineral dyes mixed in to add colour to the otherwise orange or blonde lac.
|