When the going
gets tough CEAT gets going
By
Akhry Ameer
Our vehicles have them all the time and we move from place
to place taking them for granted, and we only think of them when
they are wasted and a new set is required.
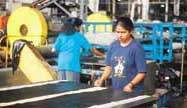
Some
of the female workers who have been recruited on a trial basis
in a predominantly male-dominated workforce at work. Pix by
J. Weerasekara
|
But
even then, to the ordinary man it is still 'rubber'. Little do we
realise that to make this circular piece of 'rubber', 15 different
raw materials are required on an average. Tour a factory and for
a good part of it you will not see this circular object, as the
Sunday Times Business recently discovered when it visited one of
Sri Lanka's premier tyre manufacturing plants, the CEAT-Kelani Associated
Holdings (Pvt) Ltd (CKAH) tyre factory at Kelaniya, the makers of
CEAT tyres, formerly known as Kelani Tyres.
While touring
the CKAH facility at Kelaniya, we are hold of processes like compounding,
drying, extending, heating, cooling, cutting, etc. and yet we see
no sign of a tyre. This is due to the fact that the various raw
materials have to be prepared into components before the actual
tyre making process begins. Most of these components once prepared
are assembled together at the stage of beading when you actually
begin to see the circular shape. The beading process brings together
the plies of rubber, the bead wire that forms the part of the stiff
edge that sets into the steel rims of vehicles and various other
components to be moulded into a bald, rounded shape known as the
'green tyre'.
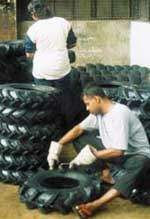
Workers
trimming the bristle-like-rubber after vulcanising in the
finished goods area.
|
The
green tyre is vulcanised to make the actual tyre we use in vehicles.
The process does not end with vulcanising as it is then sent through
the finished goods section where the bristle-like rubber surrounding
the surface is trimmed and each tyre is balanced. Finally each and
every tyre is carefully scrutinised before it is released to the
market.
One of the
unique features of the factory is its illumination, where most of
the time energy on lighting is conserved by using glass panels on
the roof to enable rays of sunlight to penetrate the premises and
provide internal lighting. Though established in 1963 the factory's
layout has been designed in such a manner that each process feeds
its output into the next through conveyor belts and suspended rails.
It is a facility
that can produce tyres in excess of the Sri Lankan market requirements.
However, this position was never achieved when it operated as Kelani
Tyres. The company became a joint venture in 1993 when CEAT of India
together with Associated Motorways and the National Development
Bank invested in the organisation that is now known as CEAT-Kelani
Associated Holdings. CEAT with a 30 percent stake has total management
control and is the technology supplier.
"The company
is at the right stage to grow." says Ramesh Ramanathan, the
Managing Director and Chief Executive Officer, confidently despite
having taken up the position only four months ago. His reasons being
the local availability of rubber, raw material at low rates of duty,
availability of a skilled labour force and the fact that the Kelani
plant has been built to produce as much as 90 tonnes per day. Currently
the plant manufactures 20 tonnes per day. The productivity or output
of tyres is measured in tonnage owing to the various sizes that
take different durations for production. The company now produces
57 different sizes of tyres of which production can carry out any
fifteen sizes on a given day.
Explaining
the low production, Ramanathan said they have been improving the
processes and are currently averaging 850 tonnes per month as opposed
to 500-600 tonnes six months ago. He added that they hope to achieve
a target of 1,000 tonnes per month by September this year. This
is expected to double the turnover of last year and hit the Rs.
2 billion mark.
He added that
at the maximum output level CKAH would be able to export around
900 tonnes after meeting the local demand. At present CKAH is exporting
to countries like Singapore, the Philippines, Dubai, Uganda and
South America. CKAH has also started to export raw materials with
its first shipment to CEAT in India recently. The company's main
aim is to achieve dominance in the local market for conventional
tyres. CKAH hopes to reach this target through a strong focus on
the trucks segment.
Asked as to
how the company can achieve this maximum output, Ramanathan said
that some machinery had been out of order and they are now in the
process of repairing them. Thereafter new machinery will replace
the ones that are beyond repair. Plans are underway to obtain new
machinery to increase output in the vulcanising process. Since the
establishment of the joint venture CEAT has introduced new machinery
including a plant to manufacture bladders. The bladders, which are
a kind of rubber, were earlier imported at high cost. The bladder
is a material that is used to hold the tyre during the vulcanising
process and does not form part of the actual tyre.
CKAH also has
a factory in Kalutara that mostly manufactures tyres for trishaws.
The company has a workforce of 700 employees including the management.
About two months ago the company recruited its first batch of female
workers on a trial basis. Formerly the workforce comprised only
males. When asked about the management-employee relationship, Ramanathan
said they are "all on one side to make things happen"
and have signed a long-term settlement with "protectivity"
(safeguards against industrial action) norms.
CKAH functions
as an independent entity in Sri Lanka and draws from CEAT in India
technological expertise and other support where necessary. A recent
development was the energy audit of the local facility carried out
by two officials from its Bombay office to explore areas of improvement.
|